If You Are Considering Testing A Geothermal Well You Need To Consider...
- Tom Weaver
- May 15, 2018
- 3 min read
You Need To Thoroughly Consider The Location Terrain and Logistics First.
You may be wasting money and manpower hours.
There may be some overlooked details to the plan as was the case when TMW Systems, LLC was approached by our client.
Here is the problem that we were able to solve for our client who was testing a geothermal pilot well that was drilled in Akutan, Alaska. They had an engineering firm provide a system schematic based on the anticipated flow rates and temperatures and were ready to engage in the manufacturing of the system. However, the consulting firm did not initially allow for a specific problem that would be incurred by the testing team – the logistics of the surrounding area did not allow for trucks of the test materials to the location.
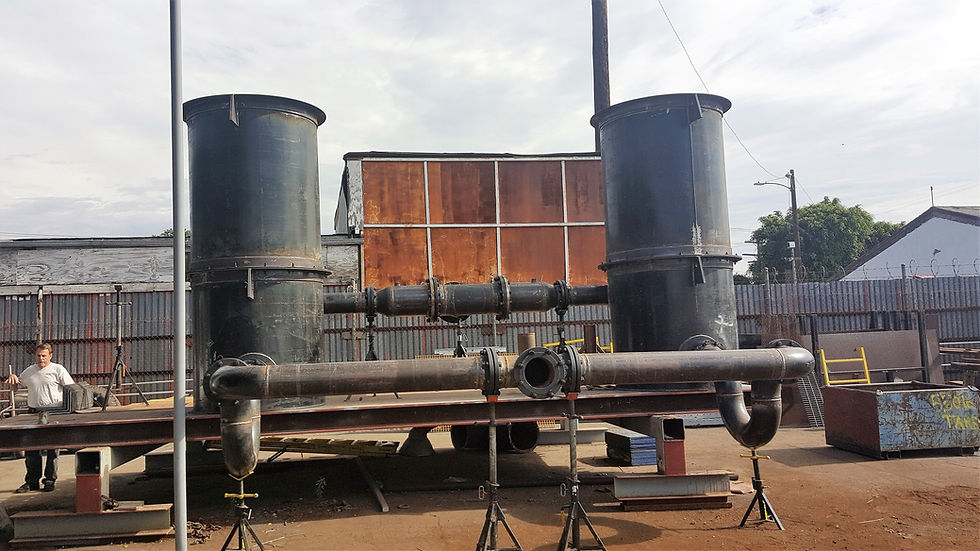
Here is the solution that TMW Systems, LLC was able to provide to our client.
TMW Systems LLC worked with our client and their consultants to redesign the system to allow for the following:
All composite pieces of the Tank farm could be transported by Helicopter to the site
All composite pieces of the tank farm could be installed and assembled by field personnel using only the helicopter in a limited fashion and hand tools
The installation process could be accomplished in a matter of days to allow for the bulk of the on-site time to be focused on testing of the well
Materials were to be standard carbon steel – A-36 plate, A-53 pipe and A-105 flanges unless specified for a particular application. We recommended the use of an abrasion resistant metallurgy (A-514) for the diverter plates since the presence of solids in the flow stream were unknown and the potential for impingement and corrosion related failure would be greatest at this point in the flow stream.
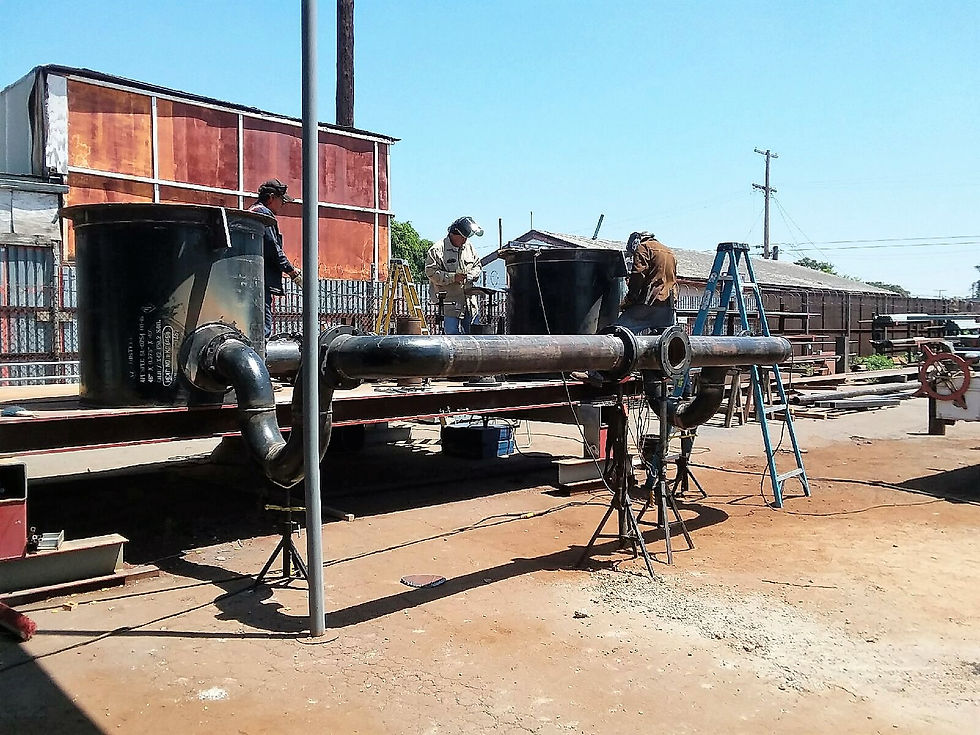
The first matter of business was the actual tanks. They would have to be sized to maintain a sufficiently slow up flow, devoid of turbulence of fluids in the tanks and have each piece weigh less than 1300 lbs for carrying by helicopter. The solution was to make each tank in two pieces that could be connected by
a roll-formed flange and custom made gasket system that would not leak in the field. Also, the internal baffles, deflection plates and down-spouts would have to be easily bolted on in the field to minimize weight of the units. Both design and fabrication needed to be tested at our location in Paramount, CA prior to shipping to ensure a tight fit and leak-proof seal.

All of the piping in the system had to be re-designed on a tight time schedule to ensure smooth, laminar flow of fluids and easy field assembly. All of the pieces of the flow system had to be easily assembled using only field man-power and hand tools. To accommodate this, TMW Systems LLC designed adjustable pipe stands that could support the weight of the flow lines when the unit was complete, but could also be used as an aid for the field personnel during assembly. These pipe stands were also created so that anchoring in concrete would not be required. The foot-print of the stands was of sufficient magnitude to prevent sinking into the ground under loaded conditions.
The testing required a weir box and a James Tube assembly for measuring flow rates. The James Tube was constructed from stainless steel internals coupled with Mild Steel flanging and piping to allow for both simple installation and accurate testing. The weir box was a custom design with both baffling and flow assurance.
Should you have an unusual or unique application, call us at (714) 371-8435 or you can always visit us on the internet at https://www.tmwsystemsllc.com. We are always ready to provide you with a free quote, leave us a message on our contact page. We specialize in providing solutions to one of a kind parts and finding unique solutions for our clients.
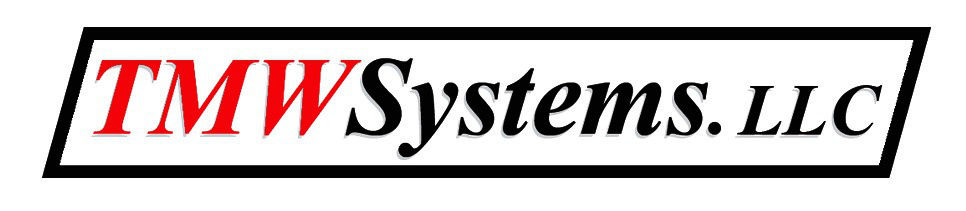
Comments